Analysis of 9 Reasons for Taps Fracture
Views : 442
Update time : 2017-06-23 19:12:15
1. Taps are with poor quality:
Main materials, tool design, heat treatment, processing accuracy, coating quality and so on. For example, the taper cross section of the transition size is too large or no design rounded corners lead to stress concentration, the use of easy to break at the stress concentration. The cross section transition at the edge of the handle and the blade is too close to the weld, resulting in a complex stress and a stress concentration at the transition of the cross section, resulting in a greater stress concentration leading to the breakage of the tap during use. For example, improper heat treatment process. Taps heat treatment, if the quenching before heating without preheating, quenching overheating or over burning, not timely tempering and cleaning too early may lead to cracks in the tap. This is also the overall performance of the domestic tap as an important reason for the import tap.
2. Improper taps:
The hardness of the attack should be too high selection of high-quality tap, such as cobalt high-speed wire taps, carbide taps, coated taps and so on. In addition, different tap designs are used in different workplaces. For example, the number of chips, the size, the angle, etc. of the taps have an impact on chip performance.
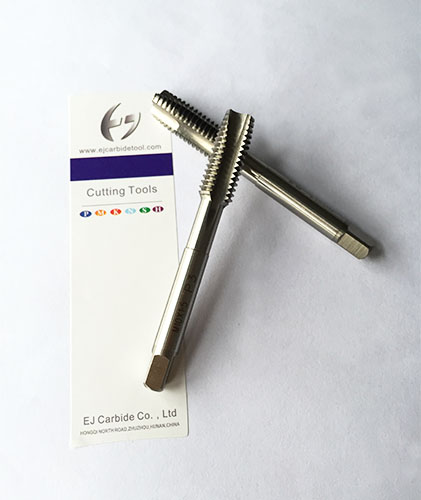
3. Taps do not match the processed material:
This issue in recent years more and more attention, before the domestic manufacturers always feel good imports, expensive, in fact, is suitable for good. With the increasing use of new materials and difficult to process, in order to meet this need, the variety of tool materials are constantly increasing. This requires the tapping before the selection of a suitable tap products.
4. Bottom hole diameter is too small:
For example, the processing of black metal M5 × 0.5 thread, the cutting cone should be used to select the diameter of 4.5mm drill bottom hole, if the misuse of the 4.2mm drill to the bottom hole, tap the tap required to cut the part of the increase , And thus make the tap broken. It is recommended to choose the correct bottom hole diameter according to the type of the tap and the different material of the attacking material. If there is no fully qualified drill bit, we can choose the big one.
5. Attack material problem:
Attack material material impure, local hard points or stomata, resulting in taps instantly lost balance and broken.
6. The machine does not meet the tap requirements:
Machine tools and clamping body is also very important, especially for high-quality tap, as long as a certain precision machine and clamping body to play the performance of the tap. Common is not enough concentricity. Tapping at the beginning, the tap started positioning is not correct, that is, the spindle axis and the bottom hole of the center line is not heart, in the tapping process torque is too large, which is the main reason for the broken taps.
7. cutting fluid, lubricating oil quality is not good:
Many domestic enterprises have begun to pay attention to this, many of the procurement of foreign tools and machine tool companies have a very deep experience, cutting fluid, lubricating oil quality problems, the processing of the product quality is prone to glitches and other adverse circumstances, while life There will be a lot of reduction.
8. Cutting speed and feed unreasonable:
When the processing problems, most of the domestic users is to reduce the cutting speed and reduce the feed, so tap the propulsion efforts to reduce the production of the thread accuracy is thus significantly reduced, thus increasing the thread surface roughness, thread Aperture and thread accuracy are no control, burr and other issues of course more inevitable. However, the feed speed is too fast, resulting in excessive torque is also likely to lead to broken taps. Machine cutting speed, the general steel for the 6-15m / min; quenched and tempered steel or hard steel for 5-10m / min; stainless steel for 2-7m / min; cast iron for 8-10m / min. In the same material, the tap diameter to take a small value, tap the diameter to take a lower value.
9. Operator skills and skills are not required:
The above problems, the need for operators to make judgments or feedback to the technical staff, but most of the current domestic operators attention is not enough. For example, when machining a blind hole thread, when the tap is about to touch the bottom of the hole, the operator does not realize that the operator is not aware of the tapping speed when the bottom of the hole is not given, or when the chip is broken, The It is recommended that the operator strengthen the sense of responsibility.
EJ Carbide offers a wide range of HSS taps,can also do high speed steel taps as customers' needs.
Main materials, tool design, heat treatment, processing accuracy, coating quality and so on. For example, the taper cross section of the transition size is too large or no design rounded corners lead to stress concentration, the use of easy to break at the stress concentration. The cross section transition at the edge of the handle and the blade is too close to the weld, resulting in a complex stress and a stress concentration at the transition of the cross section, resulting in a greater stress concentration leading to the breakage of the tap during use. For example, improper heat treatment process. Taps heat treatment, if the quenching before heating without preheating, quenching overheating or over burning, not timely tempering and cleaning too early may lead to cracks in the tap. This is also the overall performance of the domestic tap as an important reason for the import tap.
2. Improper taps:
The hardness of the attack should be too high selection of high-quality tap, such as cobalt high-speed wire taps, carbide taps, coated taps and so on. In addition, different tap designs are used in different workplaces. For example, the number of chips, the size, the angle, etc. of the taps have an impact on chip performance.
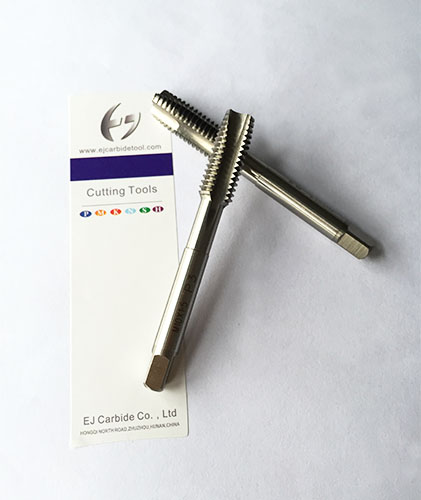
3. Taps do not match the processed material:
This issue in recent years more and more attention, before the domestic manufacturers always feel good imports, expensive, in fact, is suitable for good. With the increasing use of new materials and difficult to process, in order to meet this need, the variety of tool materials are constantly increasing. This requires the tapping before the selection of a suitable tap products.
4. Bottom hole diameter is too small:
For example, the processing of black metal M5 × 0.5 thread, the cutting cone should be used to select the diameter of 4.5mm drill bottom hole, if the misuse of the 4.2mm drill to the bottom hole, tap the tap required to cut the part of the increase , And thus make the tap broken. It is recommended to choose the correct bottom hole diameter according to the type of the tap and the different material of the attacking material. If there is no fully qualified drill bit, we can choose the big one.
5. Attack material problem:
Attack material material impure, local hard points or stomata, resulting in taps instantly lost balance and broken.
6. The machine does not meet the tap requirements:
Machine tools and clamping body is also very important, especially for high-quality tap, as long as a certain precision machine and clamping body to play the performance of the tap. Common is not enough concentricity. Tapping at the beginning, the tap started positioning is not correct, that is, the spindle axis and the bottom hole of the center line is not heart, in the tapping process torque is too large, which is the main reason for the broken taps.
7. cutting fluid, lubricating oil quality is not good:
Many domestic enterprises have begun to pay attention to this, many of the procurement of foreign tools and machine tool companies have a very deep experience, cutting fluid, lubricating oil quality problems, the processing of the product quality is prone to glitches and other adverse circumstances, while life There will be a lot of reduction.
8. Cutting speed and feed unreasonable:
When the processing problems, most of the domestic users is to reduce the cutting speed and reduce the feed, so tap the propulsion efforts to reduce the production of the thread accuracy is thus significantly reduced, thus increasing the thread surface roughness, thread Aperture and thread accuracy are no control, burr and other issues of course more inevitable. However, the feed speed is too fast, resulting in excessive torque is also likely to lead to broken taps. Machine cutting speed, the general steel for the 6-15m / min; quenched and tempered steel or hard steel for 5-10m / min; stainless steel for 2-7m / min; cast iron for 8-10m / min. In the same material, the tap diameter to take a small value, tap the diameter to take a lower value.
9. Operator skills and skills are not required:
The above problems, the need for operators to make judgments or feedback to the technical staff, but most of the current domestic operators attention is not enough. For example, when machining a blind hole thread, when the tap is about to touch the bottom of the hole, the operator does not realize that the operator is not aware of the tapping speed when the bottom of the hole is not given, or when the chip is broken, The It is recommended that the operator strengthen the sense of responsibility.
EJ Carbide offers a wide range of HSS taps,can also do high speed steel taps as customers' needs.