You know why surface roughness is 0.8, 1.6, 3.2, 6.3, 12.5?
Views : 429
Update time : 2017-10-10 21:06:52
First, the concept of surface roughness:
Tungsten carbide tools in the machining process, due to the metal surface of the plastic deformation and vibration of the machine and the cutting tool on the surface of the knife marks and other factors left on the impact of the various parts of the surface, no matter how smooth processing, as observed under the microscope, You can see the peak and valley of the situation, as shown in Figure.
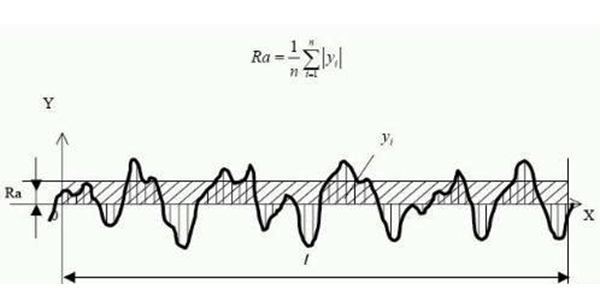
The micrographic shape features of the peak and valley with smaller spacing on the machined surface are called surface roughness. In general, the surface roughness of the different processing methods is also different.
Second, the impact of surface roughness on mechanical products:
1) Surface roughness affects the wear resistance of parts. The more rough the surface, with the effective contact between the surface area of the smaller, the greater the pressure, the faster wear.
2) Surface roughness affects the stability of the mating properties. For the gap with the surface, the more rough the surface, the more easy to wear, so that the gap gradually increased during the work; for the interference with the assembly, due to the micro-convex peak when the assembly, reducing the actual effective interference, The strength of the joint.
3) Surface roughness affects the fatigue strength of the part. Rough parts of the surface there is a large trough, which, like the sharp corners and cracks, as the stress concentration is very sensitive, thus affecting the fatigue strength of parts.
4) Surface roughness affects the corrosion resistance of parts. Rough surface, easy to corrosive gas or liquid through the surface of the micro-valley into the metal inner layer, causing surface corrosion.
5) Surface roughness affects the sealing of parts. Rough surface can not be tightly bonded between the gas or liquid through the gap between the contact surface leakage.
6) Surface roughness affects the contact stiffness of the part. Contact stiffness is the part of the joint surface in the external force, the ability to resist contact deformation. The rigidity of the machine depends to a large extent on the contact stiffness between the parts.
7) affect the measurement accuracy of parts. The surface roughness of the measured surface of the part and the measuring tool will directly affect the accuracy of the measurement, especially in the case of precision measurements.
In addition, the surface roughness of the parts of the coating, thermal conductivity and contact resistance, reflection and radiation properties, liquid and gas flow resistance, the flow of conductor surface current will have different degrees of impact.
Third, the surface roughness and surface finish the same?
Surface finish is another method of surface roughness. The surface finish is raised according to the human visual point of view, and the surface roughness is based on the actual appearance of the surface micro-geometry. Because of the international standard (ISO) convergence, China 80 years after the use of surface roughness and abolished the surface finish. In the surface roughness of national standards GB3505-83, GB1031-83 promulgated, the surface finish is no longer used.
Tungsten carbide tools in the machining process, due to the metal surface of the plastic deformation and vibration of the machine and the cutting tool on the surface of the knife marks and other factors left on the impact of the various parts of the surface, no matter how smooth processing, as observed under the microscope, You can see the peak and valley of the situation, as shown in Figure.
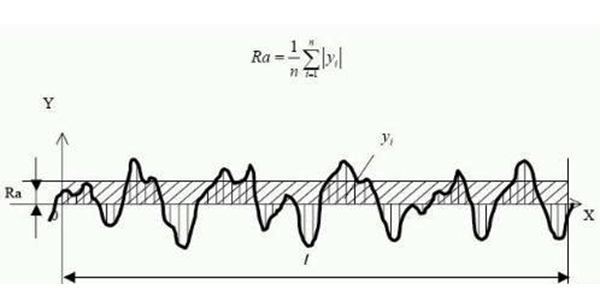
The micrographic shape features of the peak and valley with smaller spacing on the machined surface are called surface roughness. In general, the surface roughness of the different processing methods is also different.
Second, the impact of surface roughness on mechanical products:
1) Surface roughness affects the wear resistance of parts. The more rough the surface, with the effective contact between the surface area of the smaller, the greater the pressure, the faster wear.
2) Surface roughness affects the stability of the mating properties. For the gap with the surface, the more rough the surface, the more easy to wear, so that the gap gradually increased during the work; for the interference with the assembly, due to the micro-convex peak when the assembly, reducing the actual effective interference, The strength of the joint.
3) Surface roughness affects the fatigue strength of the part. Rough parts of the surface there is a large trough, which, like the sharp corners and cracks, as the stress concentration is very sensitive, thus affecting the fatigue strength of parts.
4) Surface roughness affects the corrosion resistance of parts. Rough surface, easy to corrosive gas or liquid through the surface of the micro-valley into the metal inner layer, causing surface corrosion.
5) Surface roughness affects the sealing of parts. Rough surface can not be tightly bonded between the gas or liquid through the gap between the contact surface leakage.
6) Surface roughness affects the contact stiffness of the part. Contact stiffness is the part of the joint surface in the external force, the ability to resist contact deformation. The rigidity of the machine depends to a large extent on the contact stiffness between the parts.
7) affect the measurement accuracy of parts. The surface roughness of the measured surface of the part and the measuring tool will directly affect the accuracy of the measurement, especially in the case of precision measurements.
In addition, the surface roughness of the parts of the coating, thermal conductivity and contact resistance, reflection and radiation properties, liquid and gas flow resistance, the flow of conductor surface current will have different degrees of impact.
Third, the surface roughness and surface finish the same?
Surface finish is another method of surface roughness. The surface finish is raised according to the human visual point of view, and the surface roughness is based on the actual appearance of the surface micro-geometry. Because of the international standard (ISO) convergence, China 80 years after the use of surface roughness and abolished the surface finish. In the surface roughness of national standards GB3505-83, GB1031-83 promulgated, the surface finish is no longer used.